Chillers
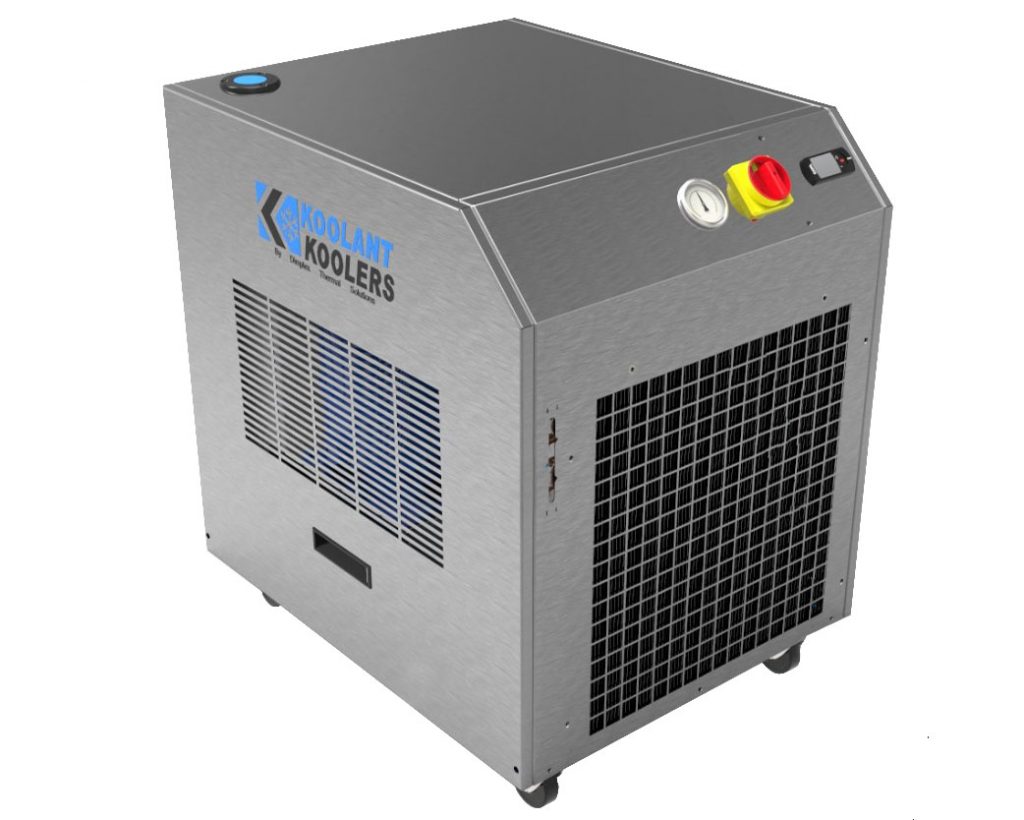
Chillers vs. Water Recirculators
What’s the difference between a chiller and a water recirculator? The major difference between the two is whether or not the unit contains a refrigerant.
An actual CHILLER will have a compressor and a pump to actively remove heat from the liquid flowing through it, using a refrigerant (much the same way a refrigerator or a drinking fountain works).
A WATER RECIRCULATOR does just that; it recirculates coolant through a radiator (much like the radiator in your car). It passively cools liquid by using a heat exchanger and cooling fins.
Do I need a chiller or a recirculator?
There is no simple rule to determine whether you need a chiller or a recirculator. If you are welding in high production, welding aluminum, or other important or exotic applications, a chiller is the clear choice. If the production rate is low, or the machine is used infrequently, a recirculator is probably fine. Please contact us for details.
Chiller Sizing
A general rule for sizing a chiller is that, for every 100KVA of welder, you should have about a 1-ton chiller. For example, if you want to cool 4 welders that are 100KVA each, you will need a 4-ton chiller. If you want to cool a 300KVA machine, you will need a 3-ton chiller. See below for further sizing details.
BTU calculations, with duty cycle taken into account
If you want a more accurate method for determining your chiller or recirculator size, you can use the formulas below.
To calculate BTU’s per hour of a resistance welder:
Resistance Welding: BTU/hr = (welder KVA) * (duty cycle) * (.85) * (.6) * 3415 BTU/hr
Resistance Welding: BTU/hr = (Welder KVA) * (Duty Cycle) * (Eff Power Supply) * (Eff Heat Collection) * 3415
Eff. Power Supply: the % of power out to power input; typically 85%
Eff. Heat Collection: the % of heat absorbed by the chilling water; Varies 50%-75% est
To calculate duty cycle:
(weld time on) / (elapsed time) = duty cycle
Example:
Say you are averaging 4 welds per minute on a 100KVA welder with a weld time of 15 cycles (250ms).
duty cycle = [(number of welds) x (weld time, in cycles)] / 3600
duty cycle = [4 * 15] / 3600 = 0.016667 = 1.67%
BTU/hr = 100 * 0.8 * 0.016667 *0.6 * 3415 = 2732 BTU/hr
Cost Savings
Historically, it was a common practice to use city water for cooling. The waste water was then run down the drain. There are a number of reasons this practice has largely gone away.
- City water can be too cold, often below dew point temperature. This can cause your electronics (SCR, diodes, transformer, IGBT, other) to “sweat”, a.k.a., develop condensation, and cause an electrical short. This is one of the more common causes of a welding system failure. (Confusingly, you may actually need to turn the set-point temperature of your chiller up as the temperature rises… which can be counterintuitive. This is to keep your chiller at or near dew point temperature).
- In certain climates, water is a quickly becoming a limited resource. You can add significant long-term costs by simply running water down the drain and paying both water and sewer costs.
Chiller Shopping Advice
A relatively new phenomenon is occurring in the (otherwise rather boring) chiller world. There is an influx of low cost chiller alternatives available through direct online sales. In one respect, this has broken up older monopolies and has brought some well-needed competition to the industry. It has also introduced some manufacturing shortcuts and “gotcha” sales tactics. Below is an incomplete list of things you should verify in the specifications before you make the leap. Make yourself a comparison chart to ensure you are shopping “apples to apples”.
- Flow Rate: Flow rate is measured in Volume (gallons, liters) over some time frame (minutes, hours, etc) . It doesn’t matter the units, but make sure you know the math to compare. Common measurements are Gallons per Minute (GPM) and Liters per Minute (LPM, possibly expressed as l/m). There are lots of tools and calculators available online to help you here. See “Pressure” below for more information.
- Pressure: Pressure and Flow Rate are very different units of measurement, but both equally important. You can have pressure but no flow (in the case of a blocked or plugged chiller). You can have flow, but no pressure, like water moving between two volumes. A water chiller needs both Flow and Pressure to be effective. Pressure can be rated in a number of units: Pounds per Square Inch (PSI), Pascals (typically kilo-Pascals or kPA), Bar (one unit of Barometric pressure is roughly 14.5PSI) are some examples.
- Heat Removal: You will see all chillers rated with a “BTU” or “Watts” (kilowatts or kW) rating. There is sometimes also a “Ton” rating. These are all the same metric. This is important to note and is typically how a chiller is sized, but beware of going by this data alone. There are a number of ways to measure this and few standards to govern the rating. A 1-ton chiller is not always comparable to another brand 1-ton chiller.
- Pump Power Rating: Pumps are often rated in Horsepower or Watts (kilowatts or kW). This can often vary widely from one manufacturer to another and is one of the “gotcha” points we urge you to review. If two chiller manufacturers claim a rating of 35PSI at 20 Gallons per Minute, but one pump is rated at half the power, beware the user.
- Reservoir Tank Size: Tank size is another factor that can vary greatly between expensive and inexpensive chillers. Though there are some “smart” smaller chillers out there that cool with a very small reservoir, a larger reservoir is going to be better in almost every respect.
- Pipe Size: Check the inlet and outlet pipe sizes. This can be a strong indicator separating a good chiller from an inexpensive one.
- Other stuff: Look for other features that may or may not be included like:
- water filter (50-micron or other)
- air intakes (a sealed system will not handle air bubbles)
- anti-backflow preventers (you don’t need this… until you do! this is a great way to get wet)
- low water alarm, water flow alarm
- flow indicator
- tank level gauge
- brazed plate evaporator (good), evaporator in the water tank (bad)
- refrigerant receiver tank (some manufacturers skip this entirely, which makes them inexpensive but unreliable)
- warranty, ask about the lead time of spare parts and who will help you when it breaks
If the sales person can not help you answer questions like these, you have to do your own homework or risk buying a new chiller in a year.
Product Videos
Image Gallery


J-Series Chillers
1/8th ton
1/2 ton
1 ton
1-1/2 ton
2 ton


S-Series Chillers
3 ton
5 ton

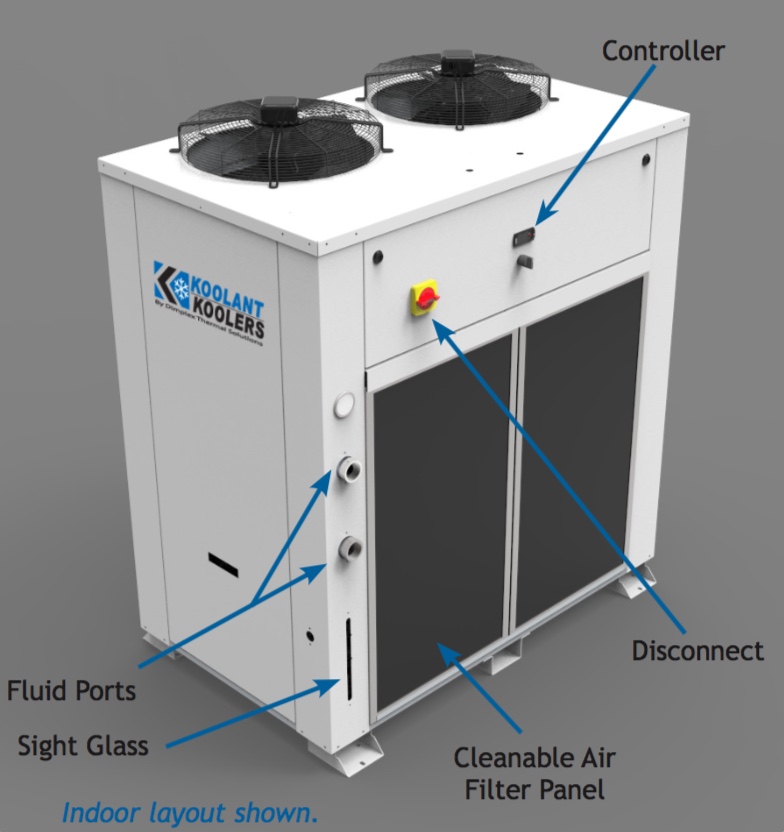
S-Series Chillers
7.5 ton
10 ton


S-Series Chillers
15 ton
20 ton